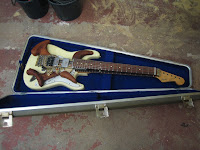
Monday 5 December 2011
Improved thigh support
The Lectus Testus has gotten a more adjustable thigh support. The fine-adjustment screw might be over the top... there's a limit to _how_ precisely you need to adjust it, but it _is_ a testbed (and it all is a hobby and supposed to be fun), so on it went anyway. The thigh support was twisted slightly in relation to the body of the guitar. Now it better follows the curve of the player's hip when sitting.
Also added was a treble side horn, giving the player the option of resting the guitar at his thigh in a "traditional electric guitar" style. Unfortunately, the thigh support is now in the way of the flexible outer cables that went from the side of the body to the thigh support, so they had to go for the moment. I might relocate them to the other side of the body.
The whole instrument functions nicely as a playable testbed. It has begun to develop some rust on the steel body, so polishing and bluing might be some of the next steps. Tuning is acceptable, but not extremely smooth. Filing and lubrication should impove that. If not, I'll have to use finer thread (M4 X 0.35).
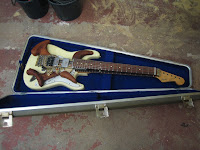
Sunday 6 November 2011
Coarse tuners part 5
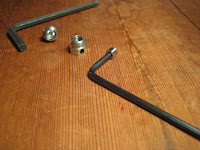
- a hex screw going through the head plate,
- an acorn nut with a hole for the string and the top cut off,
- and a hex blind screw going through the top of the acorn not, securing the string against the end of the big hex screw.
All screws have been shortened and filed flat at the end. Many other tubes, screws, etc, can be used. The string is secured at the bridge end, inserted through the hole of the acorn nut.
It seems to work nicely, but I'll have to make some more and try different string gauges.
Thursday 27 October 2011
New tuner, bridge, jack and tubing
This last month I've been improving some details of the testbed guitar:
The tuner has been changed to my slider-based design. It is mounted on an angled plate ensuring that the strings have sufficient break angle over the saddles. The angle also keeps the sliders in contact with the plate. I've used six modern strat style saddles for sliders - when I get around to it, I'll make some better (and prettier) ones from brass. Using the right screw hole for securing the string ensures that the pull of the string tightens the screw. It's got more travel than I need, so I'll shorten it around 5 mm. The knurled knobs are standard DIN 466 brass knobs. I've used two for each slider so the fingers have more grip surface. They're interlocking with one another, giving great utilization of the existing space, but making it difficult to remove one without loosening them all.
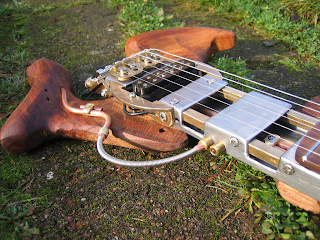
The bridge is an improvement from my earlier design consisting of two saddles each holding three strings, but is a bit simpler: It is reversed, being fixed to the body in front of the contact point of the strings. This gives me a shorter overall design, allowing for the tuner to be placed closer to the bridge.
Action is set by lifting or lowering the saddle with the small blind screws in the bottom and then securing with the big inner hex screws. Intonation is set by turning the blind screws going through the vertical flange of the saddle (they press against the big hex screws).
The jack holder is a copper pipe cap - thanks Martin for the brilliant idea. I'll use them for swithces and potmeters as well. The copper tube holds the wires, shielding them from electrical interference. The flexible cable is a piece of gear cable outer tubing back from the days when I was racing bicycles. It allows for the thigh rest to be moved and turned.
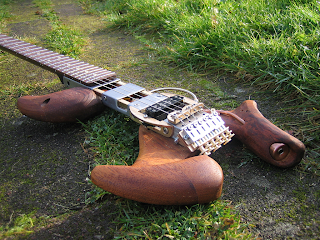
Added: I just weighed it: 2,5 kg as it is now. That's not too bad.
Sunday 25 September 2011
A guitar that works
What started as a testbed has turned into a nice, playable guitar.
For the first time, I've made a working guitar that I believe suits my position and style better than anything I could buy. This was the problem, that initially, some four years ago, got me interested in ergonomics and the possibility of building your own, very personal guitar.
That's something of a milestone, actually.
[Blogspot insists on rotating the image on the right. I have no idea why, and I can't fix it]
Things I like about the guitar:
It's comfortable to play. There's still much adjustment (and probably replacement of some wooden parts) to do, but it's more comfortable than any other guitar that I've played.
With the Seymour Duncan pickup, it sounds at least decent. My first impression is that it's a bit shrill, probably due to the steel body.
It's modular, meaning that I can replace components when I want without taking the whole guitar apart.
It's easily adjustable, making it possible to try different positions.
It's thin where it matters ...the area of the body around the bridge pickup hole is only 20 mm thick. And that's the place where it matters, because this is the area with which the guitar rests against my chest. This means that I can have it close to my body without having to reach my arms around it.
Everything on it works. Tuning, intonation, action, pickup adjustment, neck bow, etc. Some parts work really well (the bridge and wooden arm and thigh rest), while some could use improvement (the tuners and the strap horn).
The roughness and homemadeness are style elements, which are imposed by my lack of workshop skills (and the fact that I don't much like to spend money on having a professional doing it for me (because if you spend money, you have to work more, and I'm not particularly fond of that, either)). But I've come to like the roughness and the fact that you can see that the parts are made from stock metal. There's a certain honesty to it.
Things I'm doing these days:
- Playing the guitar
- Tuning the guitar (I'm dissatisfied with the tuner system, but it works well enough for now)
- Moving and adjusting the wooden pieces
- Adjusting action and intonation. That's pretty easy on the two part bridge, but I am going to make an improved version with the saddle piece at the rear, and fixing and adjustment screws towards the neck. That'll give more room for the new tuner.
Things I might do next:
- Add some copper tubing for the pickup wires.
- Copper jack cover plus master volume and switch. I plan to use the principle of copper "cups" that Rick Toone made.
- New tuner system (see picture)
- New bridge
- Make a wide copper pickup cover that covers the bridge cavity.
- Shape and smooth the wooden pieces. They're quite rough and lack a common "theme" of shapes and curves.
- Blue the body
- Test my current transformer pickups on the guitar (after all, it's thought out as a testbed)
But first, I have to buy some more tools and some more metal.
Wednesday 7 September 2011
Adding brass and wood
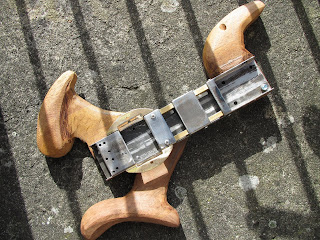
It's very easy to adjust or move the wooden pieces to allow for different playing positions. That can be useful when making other, less modular, bodies at a later time.
I'm considering a rustication process for certain areas of the wooden parts, but I have to get the guitar playable first.
Saturday 27 August 2011
Room for pickups
I decided to put one or two good pickups in the testbed guitar. My original idea was that it should be kept playable at all time. But I was too busy trying out my flat pickups to get a proper pickup mounted. I hoped that I would make a pickup that sounded great, but I'm not sure if I'm satisfied with their sound (more on that later).
I needed a good pickup for the guitar to sound decent, but also to have a sort of reference: something to compare with when trying out the various pickups. I decided to go for a couple of Seymour Duncan pickups, I bought for my first T-beam project, but later put in my strat.
The pickups are wider than the T-beam, so in order to fit them in, I had to cut through the sides of the steel box profile. That was easily done with an angle grinder (my favourite tool these days, with cutting disc as well as flapdisc for shaping wood).
So far, so good. Unfortunately, that put quite a bow in the box profile. I didn't count on that (only thought wood behaved that way), but I suppose that's part of learning.
That's put rather a halt to my progress. I'll make some brackets and beams to straighten and support the box profile in its weakened state. I was going to make pickup holders anyway, but now they're also going to add strength.
Btw, I'm condidering this oil bluing process for the box profile. And, I'm making some mahogany forearm and thight supports (and a strap horn), so I can ditch the acrylic body, that I've grown a bit tired of.
I needed a good pickup for the guitar to sound decent, but also to have a sort of reference: something to compare with when trying out the various pickups. I decided to go for a couple of Seymour Duncan pickups, I bought for my first T-beam project, but later put in my strat.
The pickups are wider than the T-beam, so in order to fit them in, I had to cut through the sides of the steel box profile. That was easily done with an angle grinder (my favourite tool these days, with cutting disc as well as flapdisc for shaping wood).
That's put rather a halt to my progress. I'll make some brackets and beams to straighten and support the box profile in its weakened state. I was going to make pickup holders anyway, but now they're also going to add strength.
Btw, I'm condidering this oil bluing process for the box profile. And, I'm making some mahogany forearm and thight supports (and a strap horn), so I can ditch the acrylic body, that I've grown a bit tired of.
Thursday 21 July 2011
Truly headless
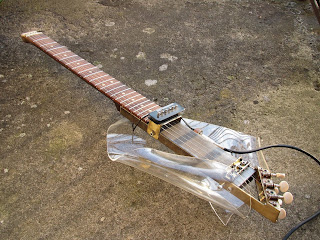
Bridge and tuners are the same as in last post. I plan to make an improved version of the tuner bracket (or perhaps abandon it in favour of one using my plunger type tuners).
The pickup is a P90 mounted above the strings. I plan on experimenting with a couple of experimental pickups using primary coils with few windings and a current transformer, but I haven't gotten around to that.
It still needs a strap to be really comfortable.
Things I might do next:
- Make a steam bent plywood body in the style of the acrylic ones.
- Make a new and more ergonomic acrylic body.
- Make a proper wooden body for the neck and ditch the rectangular steel tube for a while.
- Test and develop my pickups.
- Get back and properly finish the two-string bass. This involves adding a slidable pickup and a piezo-pickup with preamp.
Labels:
acrylic body,
ergonomics,
steel box profile,
testbed
Tuesday 8 February 2011
Two piece brass bridge
The bridge that replaces it is made from a brass U profile. It's height adjustable. To achieve acceptable intonation of all strings, it is divided in two. This makes it possible to adjust the wound bass strings and the unwound treble strings in two separate banks of three.
It seems to work fine, but I haven't tested it enough yet to judge if the design is good enough to develop further.
Sunday 16 January 2011
Future project
- Three string blues slide guitar
- For playing seated
- Sliding nut
- No strap
- Spine: 30 X 12 mm aluminium rectangular beam - freely vibrating
- Piezo pickup on aluminium beam
- Sliding pickup under strings- probably an ultra flat one with few primary windings and a current transformer.
- Plunger tuners (this principle)
- Minimalistic ergonomic body - the first version would probably be made from heat-bent acrylic plate
Labels:
ergonomics,
future project,
piezo pickup,
sketchup,
sliding pickup,
tuners
Subscribe to:
Posts (Atom)